Step by step: How to achieve a net zero building
作者
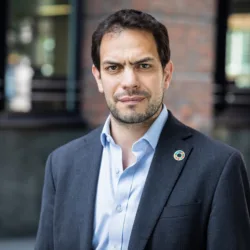
Simon Wyatt
查看个人简介
By Simon Wyatt
There’s been a lot of talk in the last 12 months about the impacts of climate change and the need to drastically reduce emissions. It has suddenly become a mainstream concern, inspiring global protest movements and myriad online campaigns, while governments around the globe are finally taking heed and setting targets for emission reductions.
For those in the built environment, particularly those of us who specialise in sustainable design, this increased level of concern is long overdue. It’s no secret that the industry is responsible for a huge proportion of emissions; 40% to be exact, and the move toward a zero-carbon future has been sluggish and fraught with perceived difficulty.
The good news is that the decarbonisation of buildings is possible. We’ve seen more action around net zero in the past six months than in the entire preceding decade, and the industry’s approach is becoming clear – particularly for new buildings.
Increasingly, clients are coming to us asking about net zero – what it means, what it looks like in practice and how we can help them achieve it. To aid their understanding, we’ve simplified our approach to net zero carbon buildings into the following seven steps.
- Passive design optimisation
Façade design is key. Utilise the useful daylight index to ensure the best possible daylight for occupants, whilst limiting artificial lighting use, reducing glazing areas, glare, heat loss, cooling loads and improving views and occupancy comfort. This enables full or partial natural ventilation for a proportion of the year, supplemented by mechanical systems to provide heat recovery in winter and cooling in summer where required. - Reduce operational energy demand and consumption
Prioritise fabric measures to drive down heating, cooling and lighting demand. Widen temperature set bands and allow occupants to adapt and control their own comfort by adjusting clothing, using fans and natural air flow. Review drivers of energy consumption to determine suitable alternate approaches that can be taken. Challenge conventional design practices and standards, recognising that the same solutions will result in the same energy intensive buildings and looking for alternative solutions. Utilise industry standards approaches like NABERS, Passivhaus and Design for Performance to embed energy savings at every stage and meet best practice energy intensity targets. - Eliminate fossil fuels
Prioritise fifth-generation heat networks and electric heat pump technologies over fossil fuel technologies to supply affordable low carbon energy. When considered in conjunction with zero emission vehicles, this will significantly improve local air quality. - Provide onsite renewable energy and storage where possible
Supply all remaining energy from on-site technologies or off-site renewable certified energy sources. - Limit upfront embodied carbon
Consider all upfront carbon associated with the initial build and restrict carbon intensity to a maximum of 500kgCO2/m2. This applies to all construction materials from extraction to installation, including the emissions associated with the construction works themselves. Use modular construction approaches, design for deconstruction using circular economy principles, and limit waste generated during construction. - Consider whole life carbon in conjunction with whole life costing
Measure all upfront and operational carbon emissions, including maintenance, fit outs, minor and major refurbishments, deconstruction and the reuse of building materials. All this must be considered over an extended design life allowing for durability and robustness. - Publicly disclose performance annually using an embodied carbon database
Use Gold Standard carbon offset schemes or equivalent to offset any residual emissions with the aim of reducing offsets over time through further onsite reductions. Publicly disclose all operational, embodied and whole-life carbon on an annual basis using an embodied carbon database like WRAP (Waste and Resources Action Programme) in the UK.
While achieving net zero in existing buildings is a much bigger challenge and one that is less clearly defined at this point, these steps are a big part of the solution for refurbishments as well. The main difference is when and how they are applied, especially where buildings have sitting tenants, MEP and cladding replacement programmes. Therefore, for existing buildings, we propose a phased approach in order to save costs and focus resources on quick wins and high impact areas. This will mean setting pathways for when these works are done and finalising an end date for when the building should become net zero.
As engineers, we strongly believe that net zero needs a technical solution and we are best placed to provide it. However, these solutions need the buy-in of the entire industry if we are to succeed in achieving the various net zero targets across the globe.
It has been heartening to see so many of our peers in construction, development and architecture, as well as our clients, start to make achieving net zero their number one business priority, and it is up to us to keep that conversation going.
We'll be going into more detail about each of the steps identified above over the coming weeks. For more information in the meantime, head over to our website to see how we can make your project more sustainable.
#YearofNetZero