Practicalities and considerations for decarbonisation
作者
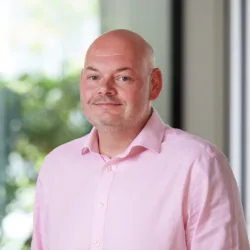
Paul Winstone
查看个人简介As retrofit moves further up the agenda for the built environment, it has become crucial for engineers to understand the nuances and complexities of designing building services systems that integrate into existing buildings.
Whilst the comprehensive refurbishment of buildings is nothing new, trying to balance the multi-faceted approach of designing to achieve the low energy usage intensities required for net zero carbon status presents some unique challenges. Considerations such as minimising the extent of embodied carbon by maximising the retention of existing services whilst keeping the building live need to be taken into account.
Our team of building performance services engineers have been at the forefront of retrofit, undertaking projects from early-stage assessments and feasibility studies to the actual delivery of best-in-class buildings.
Over the course of our journey, we have encountered some of the more common considerations that regularly crop up. Below we explain them in more detail.
Power availability
It's fair to say that one of the first questions that gets raised when we look at replacing gas fired heating systems to all electric, is whether there is enough power.
Like most things, it depends. Typically, if a building was originally used as an office, then it tends to be cooling-led, therefore predominately the largest consumer of electricity was associated with a chiller plant. With the reduction in power densities from lighting and small power loads over the years, typically the adoption of a heat pump-based system is on parity with the provision of cooling via chillers with no significant change in electrical infrastructure required.
In different building types such as residential, schools or any other that aren’t normally comfort cooled, it’s highly likely that the electrical infrastructure does not have the capacity and an upgrade will be required. Given the time frames and costs involved, this is something that should be flagged early in the project.
Lease obligations
Undertaking a comprehensive refurbishment of a building whilst it’s occupied and in use isn’t impossible. It does, however, require working in a phased and strategic manner, often with large tranches being undertaken out of hours. Unsurprisingly, this extends project programmes and makes the project more expensive than if the works were undertaken in a vacant building. It's worth looking at lease events for the building in question to understand if there’s a period when the building will either become partially or even fully vacant and defer the project until then.
If the building is let, then when replacing the building’s heating and cooling, provision needs to be undertaken sympathetically with respect to the tenant’s agreement for lease. That often stipulates power densities as well as operational characteristics of the base build systems, both of which can be affected by the adoption of heat pump-based solutions. Deviating from these will potentially involve having to renegotiate leases midterm, something that typically a landlord or tenant would like to avoid.
Phasing and sequencing
As mentioned, it is possible to undertake comprehensive refurbishments whilst the building remains live by carefully phasing the works, so that modifications to heating systems occur during the summer season when demand is lowest. It works the same with cooling systems during winter months.
Site constraints and logistics
As designers we often been guilty of focussing on what the final iteration of the design looks like, with little consideration for the working life of the building. Shoehorning plant into every nook and cranny and lifting large heavy pieces of equipment on tall buildings may be fine during the initial construction when there happens to be a tower crane available, but 20 years later it is a somewhat different proposition.
Whilst every good designer should pay cognisance to future plant replacement during the design stage, it is often an afterthought. Although minor or component replacement for capital plant is often considered, it's unlikely people were envisaging the cranage of multiple large and heavy heat pumps onto the roof of buildings midway through a building's life cycle.
Similarly with large built-up developments often demanding road closures, which often must be applied for many months in advance, final location of plant with respect to programme needs consideration especially when being undertaken in seasonally as outlined above. I know of at least one decarbonisation project where the client had to erect a tower crane temporarily to get plant on the roof of the building as the local authority would not grant a road closure.
Some of these challenges can be mitigated by considering the type and arrangement of plant, noting that plant disposition when retrofitting a building is usually one of the biggest challenges. For example, cascade heat pumps versus air source or adopting a modular approach with multiple smaller machines in lieu of larger units.
Retention of services; embodied carbon vs fit for purpose
In theory, the retention and reuse of elements of a building makes perfect sense. After all, why scrap an entire pipework distribution only to replace it with a near identical arrangement? The same applies with ductwork and ancillary plant items, such as pump sets and various motor control and electrical panels, all of which can be cleaned, refurbished, or overhauled whilst retaining most of the equipment.
Adopting this as a strategy greatly reduces embodied carbon and arguably highlights programme efficiencies. So, a win, win? Unfortunately, a degree of diligence needs to be undertaken with this approach. Namely, are the services we are looking to retain in good enough condition in the first place and won’t risk compromising our freshly installed plant?
Pipework systems typically have a life expectancy of more than 40 years and given that the typical lifecycle of a building service installation is circa 15 years, the pipework should have the potential for reuse for several iterations during the building’s life. However, this assumes the systems have been looked after. If water quality has been problematic historically, then risk of contaminants being present can be catastrophic to new plant installations.
A lot of the risks associated with retention and reuse can be identified early on with comprehensive validation work which will often require specialist input and should be undertaken during the project's early stages. As an example, water sampling across piped systems will give indicators of the internal condition of pipework and the risk of contamination and potential to reuse.
Compatibility
Compatibility in this context relates to the operating characteristics of the new plant installation in comparison to what we are replacing.
If the intention is for a full building refurbishment, this isn’t an issue as the new equipment will be selected accordingly. However, if we are intending to retain the existing installation then considerations need to be given to what the base design was originally selected on versus what the new plant can achieve. If the gas fired boiler installation was designed on primary temperatures of 80°C / 60°C, then utilising an air source heat pump that can only work efficiently up to 45°C, is going to be problematic with respect to the existing equipment, pipework distributions and terminal units. If this is the case, then a cascade arrangement with a higher output (circa 65°C whilst still maintaining good levels of efficiency) would be more appropriate.
We have seen and produced lots of analysis on the performance of coils selected on higher primaries and the effect of utilising lower temperatures, which in most cases result in an acceptable decrease in output. Typically, that's the case of fan coil units, being of no consequence due to the historic oversized nature of the heating coils.
However, this isn’t the only consideration. We need to consider systems holistically, for example, are the existing control valves suitably sized? Usually these are sized on a low flow condition because of the oversized nature of heating coils. If we double the flowrate, will they still operate correctly? All the supporting and ancillary systems that are intrinsic to the correct operation of a building needs to be reviewed with the same vigour so that works can be factored in and captured as part of the project during the early stages and not when the problem arises on site…
In conclusion
We know that the rush to reposition assets due to market pressure or upcoming legislative changes means that the problem of decarbonisation in retrofit can seem daunting or appear expensive and disruptive, however, we are firm believers that every problem has a solution, and with the right team and approach, these solutions do not have to come at a premium.