Gas to electric – The challenges of making a building net zero carbon
作者
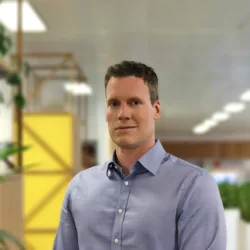
Robert Marney
查看个人简介Delivering energy efficient buildings is what we do every day at Cundall. But, the bar has now been raised.
The signing of the Paris agreement in 2015 has started the drive to limit greenhouse gas emissions so that temperature rise remains below 2 degrees Celsius, and ideally below 1.5 Celsius by 2050. As a result, just delivering energy efficient buildings every day is no longer enough. According to the definition proffered by the World Green Building Council in net zero buildings, we must now deliver “highly energy efficient buildings which generate or supply the energy they need to operate from renewable sources to achieve net zero carbon emissions”.
The above statement takes gas, as a fossil fuel, straight out of the equation, and based upon the continued decarbonisation of the power supply grid, this puts electricity firmly in the frame. Most people believe that as building plant and equipment becomes more efficient, electrical loadings reduce. They would be right to think this.
However, in a building that has gas fired heating and hot water, the obvious solution is to remove the gas and install electric heat pumps to provide this service instead. Suddenly this places a large electrical demand on the available existing building electrical supply, and the increase could be enough to warrant a substation or significant supply enhancement. That makes for sobering news if a substation wasn’t planned for cost or programme-wise, let alone the impact on ground floor space at the building perimeter that would need to offer unimpeded 24/7 access from the street to comply with the network operators requirements for a substation.
Refurbishing an existing building offers a lower embodied carbon solution than building a new one due to the inherently high embodied carbon of building a new structure and building envelope. It presents a greener option than a new build upon suggestion, but refurbishments of existing buildings have always had challenges for MEP designs.
Services engineers will face the challenge of trying to reuse existing riser spaces (vertical shafts that contain pipes or wires) when net lettable space comes at such a premium. That is fine until the client wants to increase the building occupancy and those existing risers (and the services in them) have to work harder. The services then usually become larger in order to meet the brief and achieve greater levels of energy efficiency (e.g. larger ductwork equals less resistance and therefore has a lower operational energy requirement).
Similarly, issues with retaining and reusing a façade will present challenges that need to be navigated when trying to achieve net zero carbon targets. Optimising solar gain and improving building fabric thermal performance often have considerable capital cost and planning implications but are an essential first step in reducing internal heating and cooling loads through passive improvements. Early agreement on building fabric improvements will help crystalise the performance required of the heating and cooling plant, and in turn inform selections and sizes.
Electrical engineers have the specific issue of reusing the existing building electrical supply and avoiding any costly power supply upgrades/enhancements – especially if that increase in demand would push over the 400A threshold and require a new substation (small/medium buildings) or even an additional transformer (larger buildings). This kind of thing is not news that clients, quantity surveyors, or architects want to hear. With cost and programme impact considered it has the potential to make projects unfeasible.
On a recent project, Cundall had to make early notional plant selections and produce detailed electrical load calculations at Stage two – this was to help identify the viability of removing gas from the building. This is an example of work required in advance to de-risk a project whilst pursuing a client net zero carbon aspiration. In this case, the client was nervous but we were able to reassure them by doing the early work and explaining where the issue had arisen, the risk, and the process to mitigate it. This challenge is coming up more and more on projects and is not going away any time soon.
There are some things we can do if we are presented with refurbishments of existing buildings:
1. Identify the risk to the client as soon as possible.
2. Go to site early on in the project and confirm the existing building electricity supply with the network operator.
3. Determine the façade proposals and building fabric upgrades.
4. Undertake detailed electrical load calculations earlier than usual.
5. Make notional low energy high efficiency plant selections (to feed into the electrical load calculations) earlier than usual.
6. Ringfence the specification of low energy plant to prevent contractor Value Engineering, if higher loading plant would exceed the maximum demand.
7. Always push for onsite renewables that will lower electrical demand of the building.
The above list is not exhaustive but it’s a good start. It requires us to alter our working practice slightly but for a good reason.
As we continue on this net zero carbon pathway, the people and teams we work with will become more familiar with the challenges and the associated solutions. In the first instance, continued communication with the client and the design team is key and awareness will grow as we all become more familiar. Failure to communicate will keep people in the dark during the design process, whilst early engagement with the team and client, and continued communication, paves the way to informed design decisions and harnesses the value of closer collaborative working. After all, collaborative working and problem solving is central to what we do at Cundall – this new net zero chapter is an exciting opportunity for all of us to practice and master that.