Digitally delivering on the triple bottom line
作者
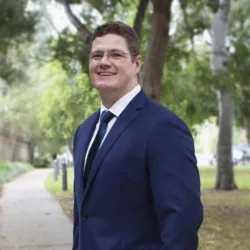
David Collins
查看个人简介The ‘triple bottom line’ of social, financial and environmental sustainability is very much aligned to the holy grails of best practice design and construction – time, cost and quality. For example, when the workplace is safe, inclusive and efficient, people tend to be happier, more productive and more likely to stay with the business, which addresses some of the common themes of social sustainability (the “S” in “ESG”).
Better management of construction costs is obviously contributing to financial sustainability and good governance, and quality work means reduced waste and a more robust building outcome, both of which deliver on fundamentals of sustainability.
Despite the simple logic, however, the Australian industry does remain challenged in achieving these things consistently. The recent review by the Australian Construction Industry Forum (ACIF) of progress on the Shergold and Weir recommendations shows that regulators also are still behind the curve on progress. Similarly, the pushback on the 2022 changes to the National Construction Code shows there are many industry stakeholders still willing to shortchange themselves on quality and sustainability using financial considerations as a rationale.
This is not an argument that passes the pub test. If we improve the processes that shape design, procurement, delivery, commissioning and handover, then projects quite obviously save on time (which costs money), material costs (which cost money) and rework and defect rectification (which also cost money).
Making the link between process and outcomes
Many of the initiatives that improve the environmental performance of a project are the result of decisions around design and procurement, works staging, quality of workmanship and robust inspection and test plans (ITPs) from all subcontractors. In short, achieving NCC 2022 level performance or the next stage, true net zero and optimised energy efficiency, can be achieved within project margins if the right decisions are made.
While it is not the entire silver bullet to enable this shift, the use of technology enables cost, time, quality and sustainability to be simultaneously addressed and measurable gains achieved. There are the basics most building information modelling (BIM) users are familiar with such as improved project coordination, enhanced clash detection, reduced rework and streamlined project scheduling, but we can also take it up a notch with other tools in the digital design and construction kit.
Practical examples
For example, the use of digital-first parametric design facilitates the most efficient use of materials and optimal spatial planning. This design approach uses software that can integrate with BIM, and reduces waste caused by over-specifying and over-engineering.
The general value of parametric design is it takes as inputs the primary requirements for project specifications (including code and standards requirements) and produces options that will meet them. The human smarts then come in to sift through the parametric outputs and select the most appropriate and buildable option.
Digital modelling can also take the guesswork out of thermal performance and energy performance, and the outputs can also be linked with the BIM model. This suite of project excellence enablers includes computational fluid dynamics modelling to show how factors such as daylight, airflow, heat transfer and cooling will interact within a proposed building envelope, based on parameters including local climate, orientation, glazing specifications, roof and wall systems and so forth.
This gives the design team an opportunity to fine-tune specifications and construction approaches for optimised energy performance, daylighting, acoustics, natural ventilation and thermal comfort.
Digital technology assists also with generating data on embodied carbon in materials. This is extremely valuable for contractors working with developers who are pushing to reduce their carbon emissions including their indirect Scope 3 emissions. Through understanding, measuring and minimising material and construction emissions, both contractor and client achieve environmental and commercial benefits.
Getting early runs on the scoreboard
The best part is this data can be captured at the design stage – the point at which it is least cost to make adjustments to materiality, structural design, program or building services engineering design. So, if the modelling shows a project approach will not deliver on either the conventional bottom line or the new carbon-conscious bottom line, teams can collaborate to find a solution quickly and efficiently.
We have successfully used this approach to support delivery of net zero-ready, all-electric assets across asset classes including retail, industrial, aged care, commercial office, data centres, residential and institutional buildings.
Already the leaders in the design and construction sector are levelling up to the full digital toolkit and using it to match the priorities of clients that are demanding built assets that are future-fit for net zero, full electrification and reduced lifecycle carbon emissions. With global finance also heading in this direction, the Australian building industry needs to step up, upskill and appreciate the wider benefits for the triple bottom line.
Better management of costs, improved project efficiency and productivity, demonstrated gains for social and environmental responsibility – it’s a recipe for creating value for everyone in the construction supply chain.
This article was first published at Sourceable